またひとつiBの夢が叶いました!(2/3)
KAWASAKI マッハ 750cc H2 ビレット(削り出し)シリンダー製作過程。

ただのアルミの塊から完成部品のシリンダーを削り出してしまう!
それはiBの夢でした。
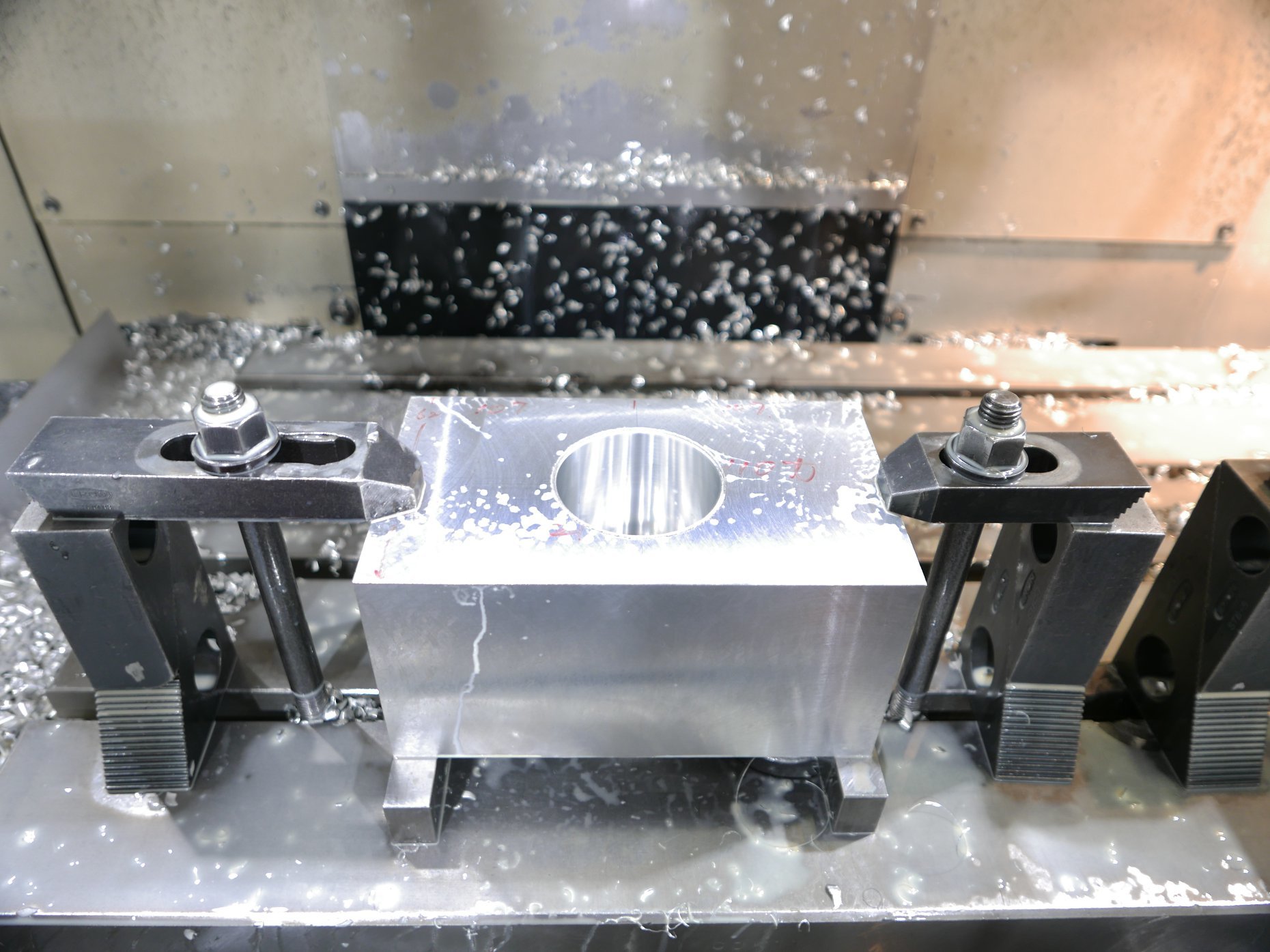
それには3D CAD/CAMの技術を欠くことができません。
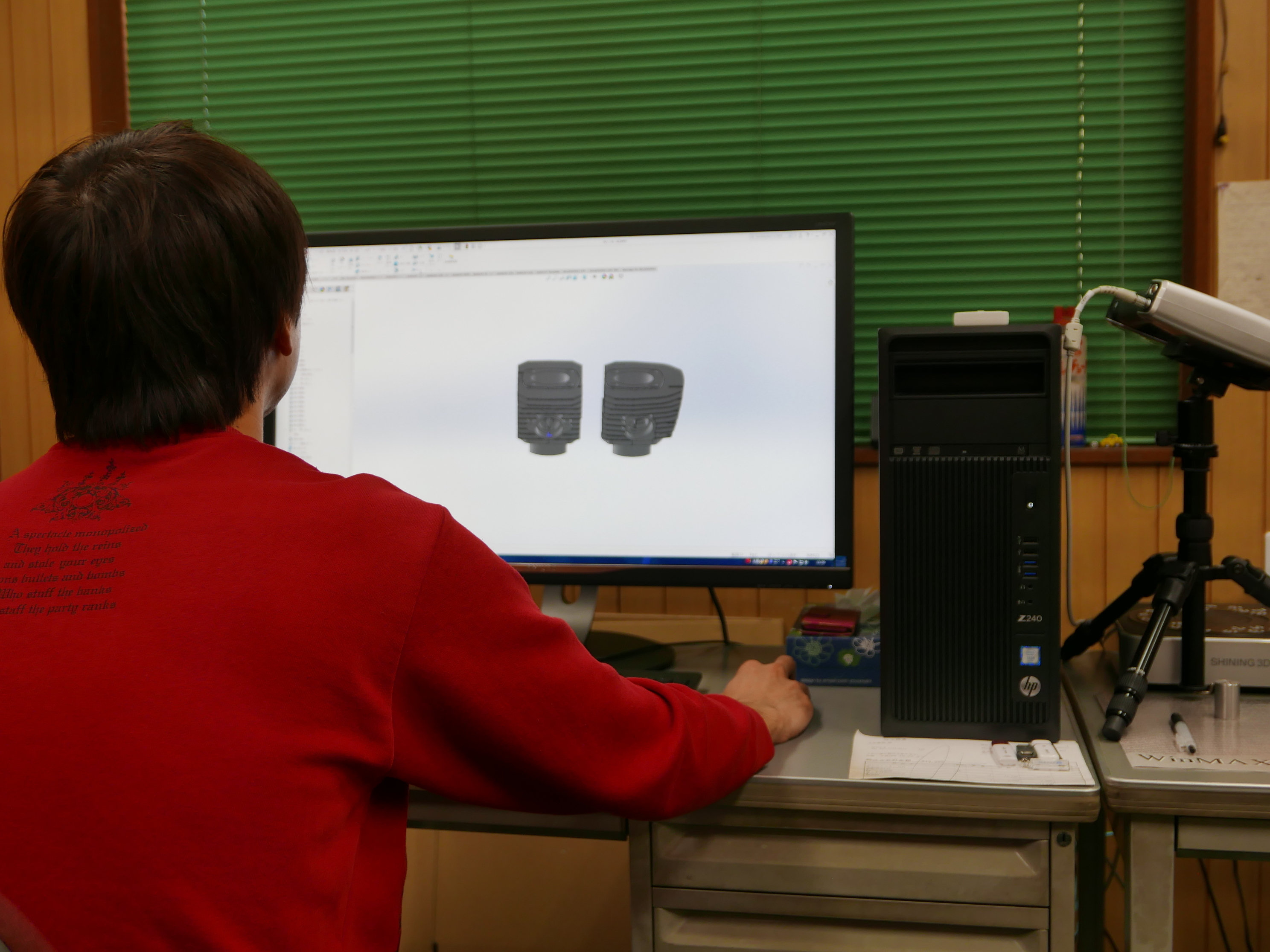
3Dスキャナーやワークステーションを導入し、3DCADソフトにはSolid Worksを採用しました。
3DCAMはSolidCAMです。
吉澤技師がこの3年以上にわたって研鑽を重ね、この技術に磨きをかけてきました。比較的単純な形状から始め、2ストロークのポートのような複雑形状もこなして、いよいよH2の加工に取り組みました。
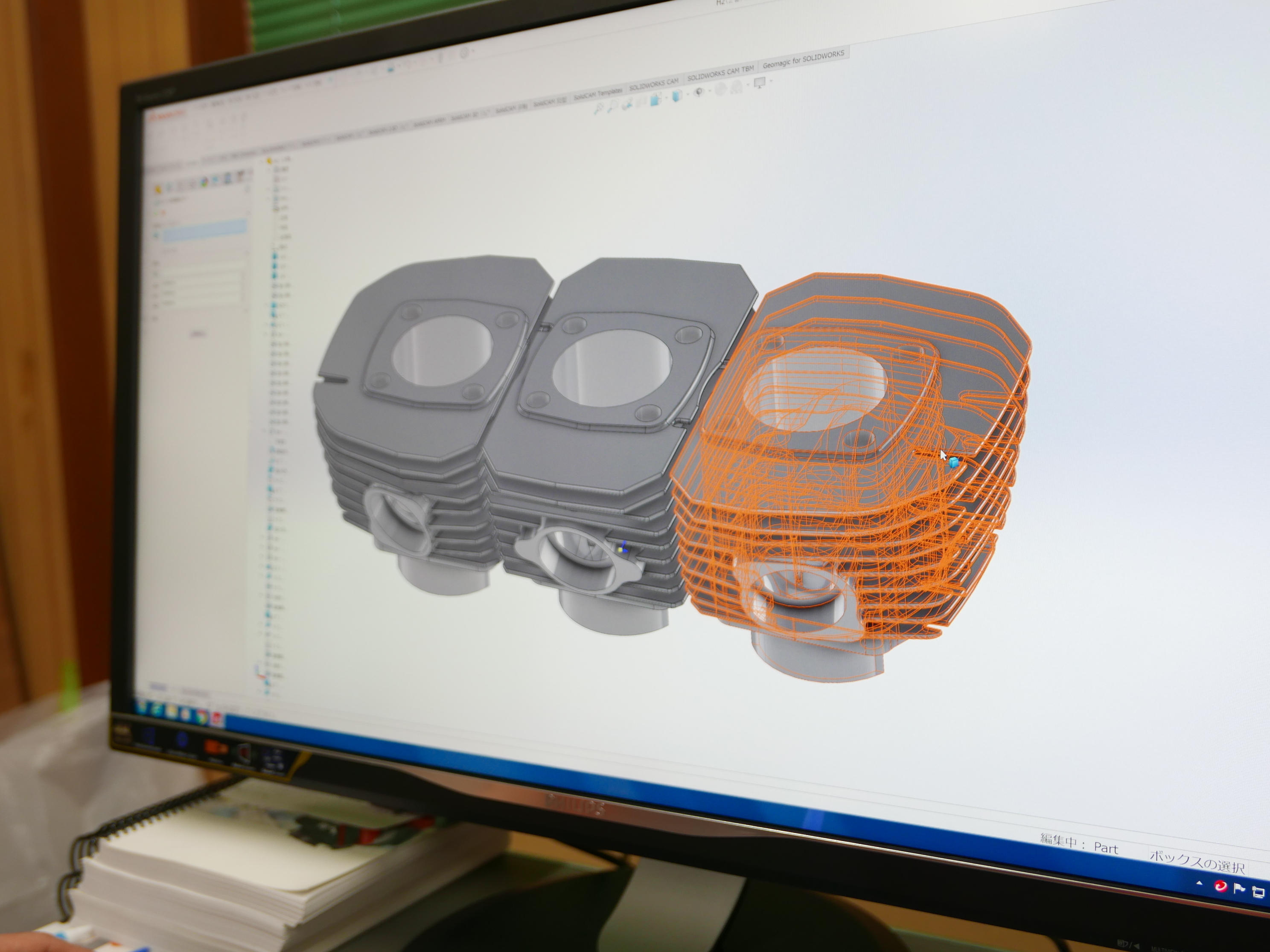
ポートなどに加え、H2のような空冷のシリンダーでは空冷フィン部分がモデリングの上でも加工をする上でも大きな問題になりました。
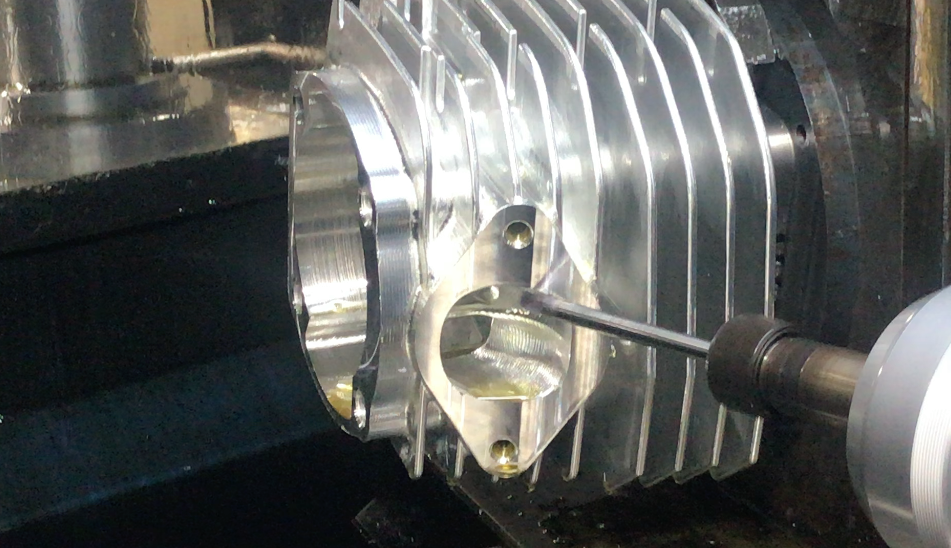
通常業務で忙しく稼働する横型マシニングセンターが空く隙を狙って作業を進めたため、試行錯誤を繰り返しながら3個のシリンダーを削り出すには2年の月日がかかっています。
優秀な技師である吉澤技師が、そんな利益を産む見込みもたたない技術の習得に多大な時間を費やす、ということには社内でも賛否がありました。でも、吉澤技師は熱心にこの仕事に取り組んでくれました。それはこのような技術習得が吉澤技師自身の希望にも合致していたからです。
そして、とうとう削り出しには成功し、2019年3月にはモーターサイクルショウのブースで展示を行い、人気を博しました。ただ、この時はまだスリーブは入っていません。
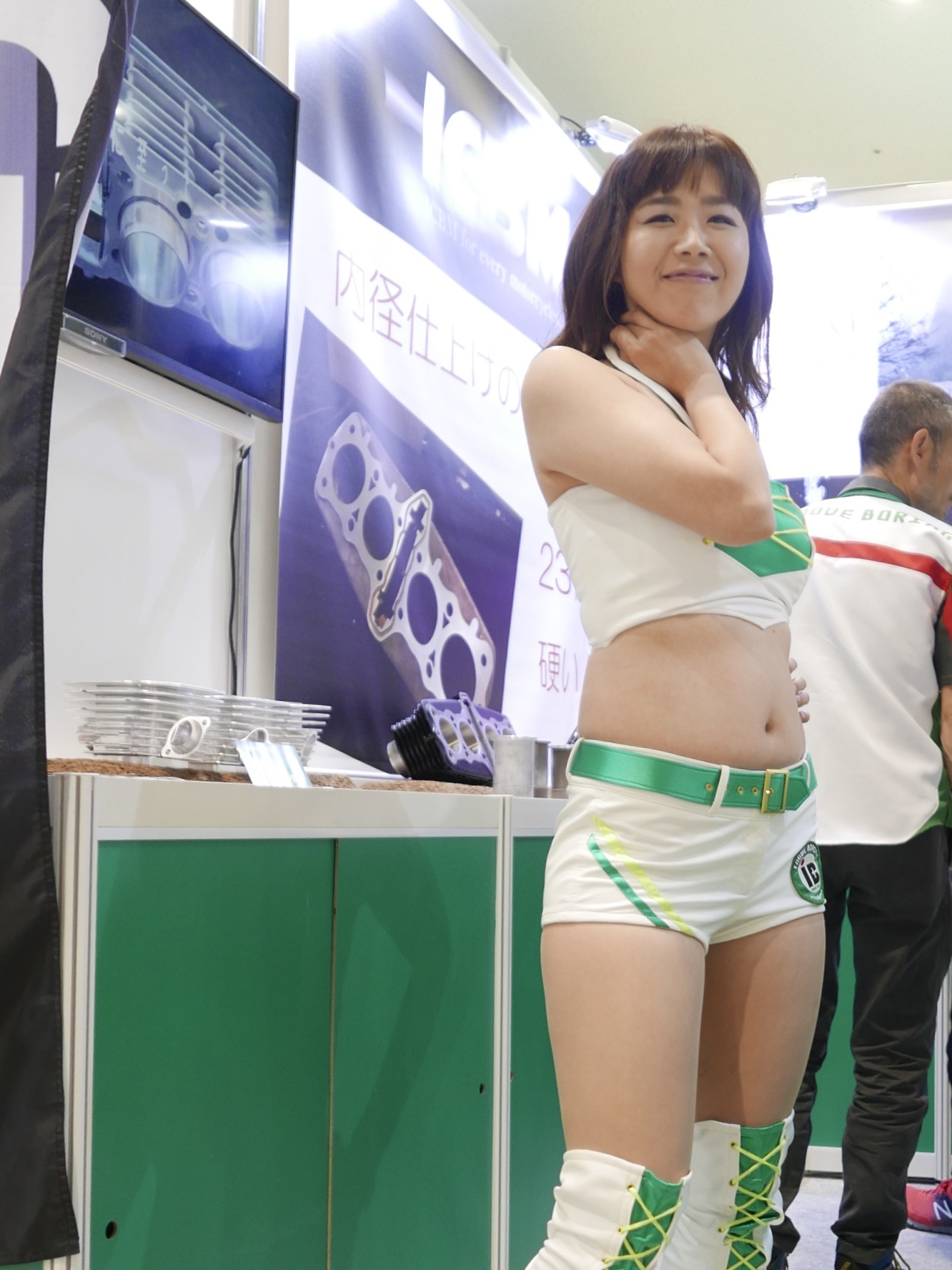
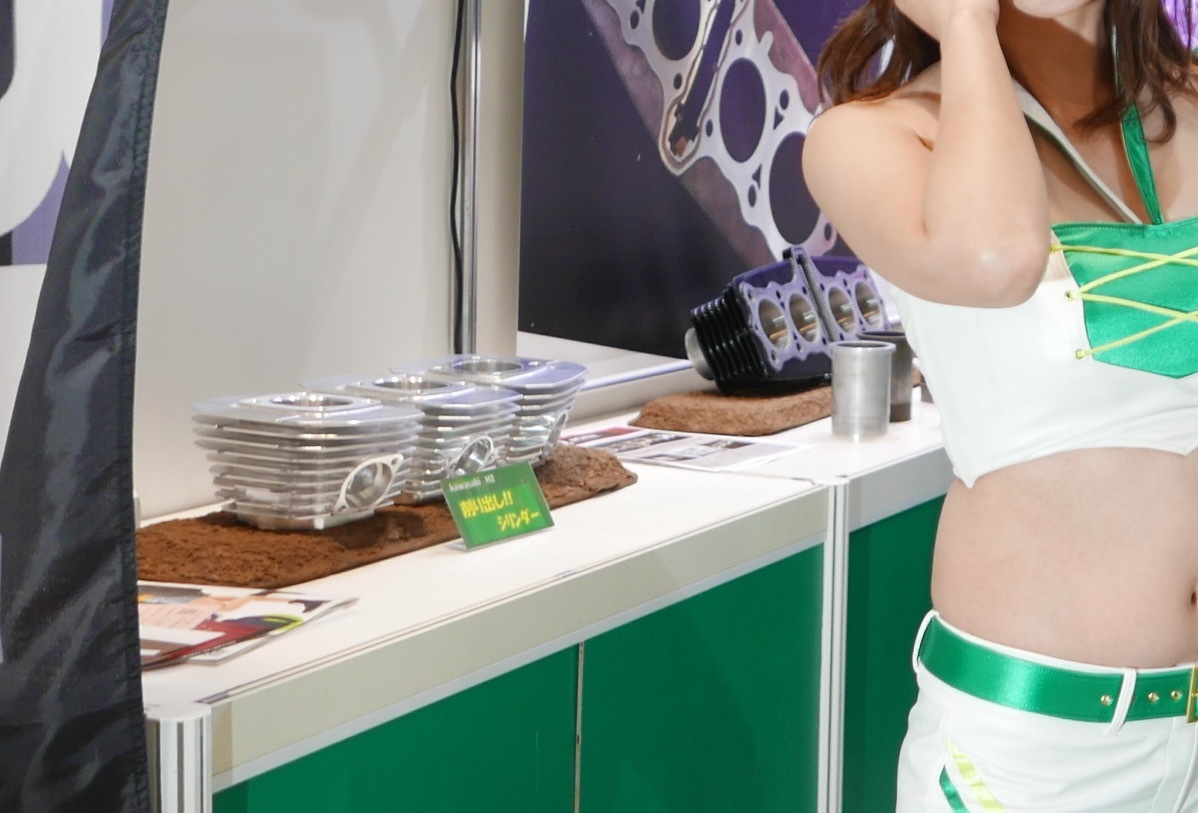
内径に挿入するICBM®アルミメッキスリーブについては、最近は毎月4〜5台の受注をいただいているので、なんら苦にはなりません。

完成したアルミメッキスリーブを挿入し、ついにH2ビレットシリンダーが完成しました。

ただ、今までの製品とは違いiBが一から設計3Dデータ作成、そして加工完成までをやったものですので、寸法通りできあがったからそれで完成としていいのかどうか。シリンダーとして実際にオートバイに載せてエンジンを回しテストする必要があるのではないか。そういう意見が出ました。
そこで、2ストロークマガジンの後藤編集長に特にお願いして、いつもレースで使っているH2レーサーをご提供いただいてテストをすることになったというのが、今回の経緯です。
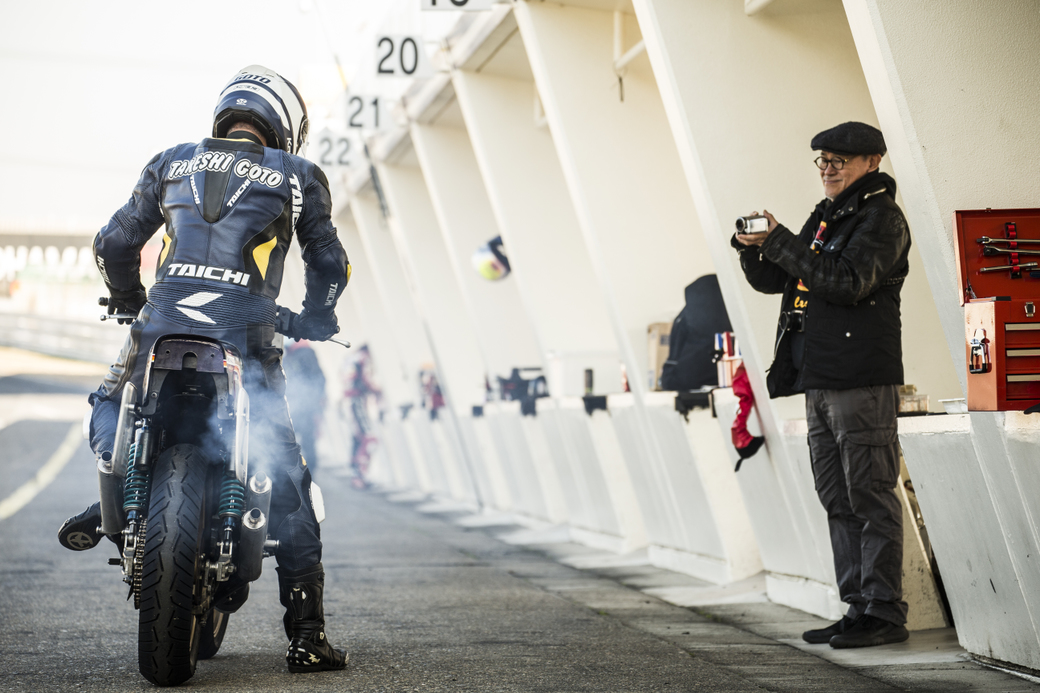
さあ、はたしてiB初の削り出しシリンダーは無事にサーキットを走れるのでしょうか。
--Part3へ続く